Insights
Factory made Houses – A solution to Kenya’s Low-Cost Housing, and available opportunities
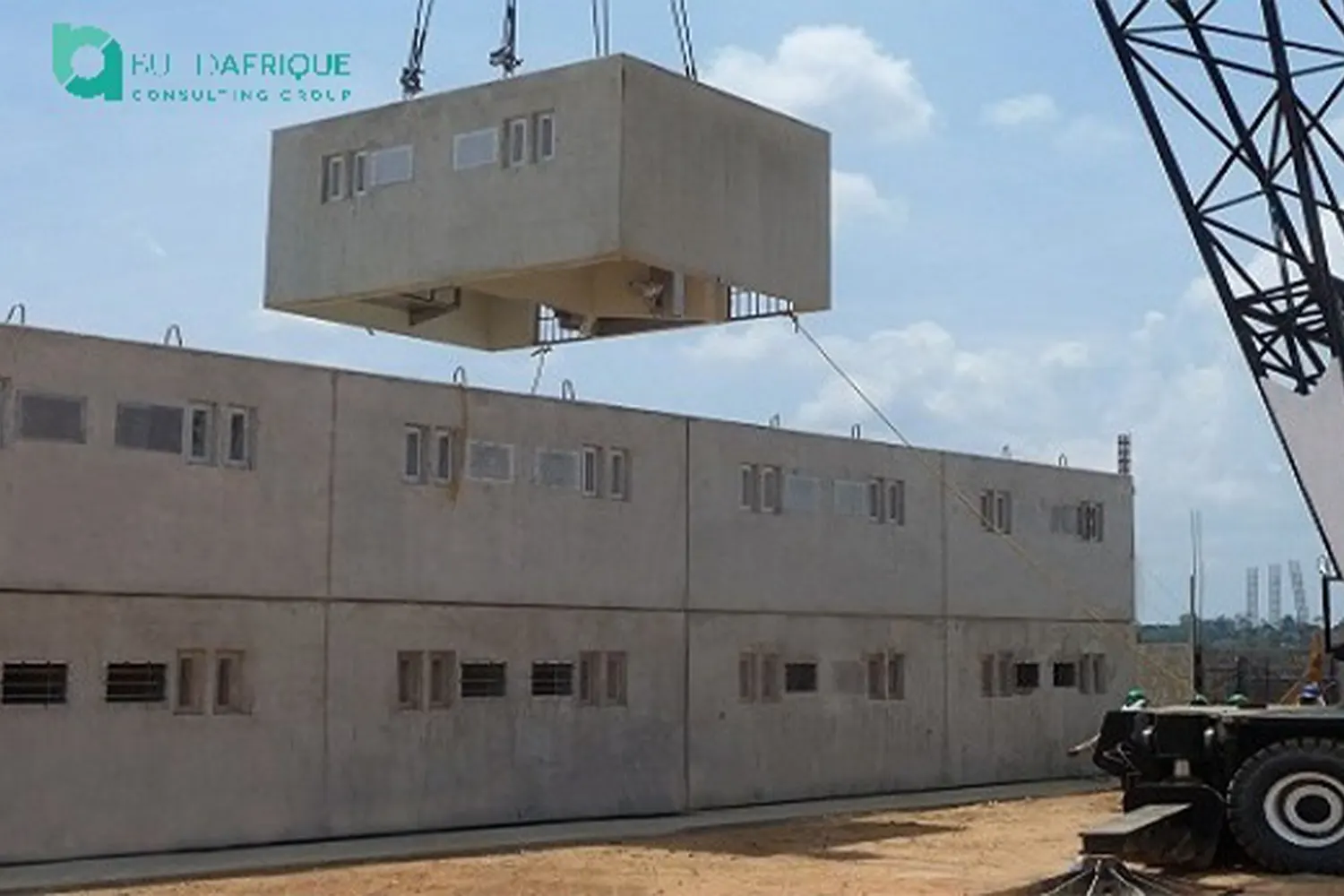
Factory made homes refer to buildings constructed in components, modules or movable sections. They may also be used to refer to mobile homes. Factory made homes are built onto steel beams and are then transported in complete parts to the home site, where they are assembled. Wheels, hitch, and axles are moved on site where the home is placed on a permanent foundation.
In Kenya, factory-made homes are used as temporary housing structures for construction workers. However, building professionals, institutions and corporations in the property sector are of the idea that the EPS technology –expanded polystyrene technology and prefabricated houses – could help resolve the low-cost housing deficit currently in Kenya. Although the initial investment cost of EPS is arguably high, the technology is seen as an alternative to contemporary building methods, if improved for cheaper prefabricated materials, as it requires less construction time, cutting down up to 60 percent of time used to build a contemporary house.
A single panel with measurements of 1.5 m by 3 m is estimated to cost approximately Ksh 8000 in production in the year 2018, without factoring the initial investment cost of putting up the production factory infrastructure. A standard two-bedroom house measuring about a hundred square meters requires about 70 boards, which translates to a total of Ksh 560,000 for an entire home. With the cost of construction down to this level, Kenya’s housing deficit, which currently stands slightly above 200,000 units annually against a supply of 40, 000 units can be resolved, of course with cost incentives playing a huge role in setting up the production factory infrastructure which has been argued to be costly.
The construction of a factory made home typically involves linking plumbing and electrical lines across sections, and sealing two sections together. They can be single, double or triple wide, depending on the width of the outline sections. If designed correctly, they can be difficult to distinguish from a stick-built home for the untrained eye. The most notable difference between conventional building and factory made structures is in the nature of construction. Traditional building involves transportation of all building materials like timber, brick, and cement for construction at the site. In factory-made homes, only the foundation is made this way. While factory-built homes eliminate transport expenses and development costs, this is not all. With these homes, one is guaranteed on the safety of workers. Furthermore, one does not have to worry about waste as construction materials can be recycled into various uses.
One of the most important things to watch out for in manufactured homes is drywall cracking. This is mainly apparent after a house has settled onto its location attributed to changes in temperatures or humidity; factors that may have adverse effects on the overall effect of dimensions in building materials. To avoid this, buyers should ensure that a reputable and honest contractor positions the initial set-up correctly. It may be important to ensure that contractors are not learning on the job.
As the idea is still not understood by a majority of the population, much may need to be done to promote factory-made homes as a secure investment option. If Kenyans can adopt the idea of manufactured homes, housing rates may reduce tremendously. In developed countries, factory made and modular houses are a widely accepted type of housing. One of the most notable structures in the world is the Sweel Track in England which is the oldest roadway built by use of pre-assembled timber. Its construction dates back to 3800BC.
On available opportunities, the Kenya Government is set to roll out its ambitious low cost housing plan for the next five years, through partnership with private developers and investors. Private developers wishing to partner in this development initiative therefore have an alternative building solution in factory-made homes. Already, some foreign investors are beginning to set up trial factories in Kenya, with a hope of rolling out the technology in Kenya to meeting the high demand for housing. Prospective Home Owners also have a chance of buying into these houses, which are expected to fairly priced.
Related
Insights
Real Estate Quantity Surveyors and Cost Consultants In Kenya
Buildafrique is a Quantity Surveyors Company in Kenya Real Estate and Development and…
Quantity Surveyors Services Company in Kenya – Nairobi, Thika, Nakuru, Mombasa and Kisumu
Buildafrique are Quantity Surveyors and Construction Cost Consultancy company in Kenya…